Die Casting Parts Factory: Revolutionizing Metal Fabrication
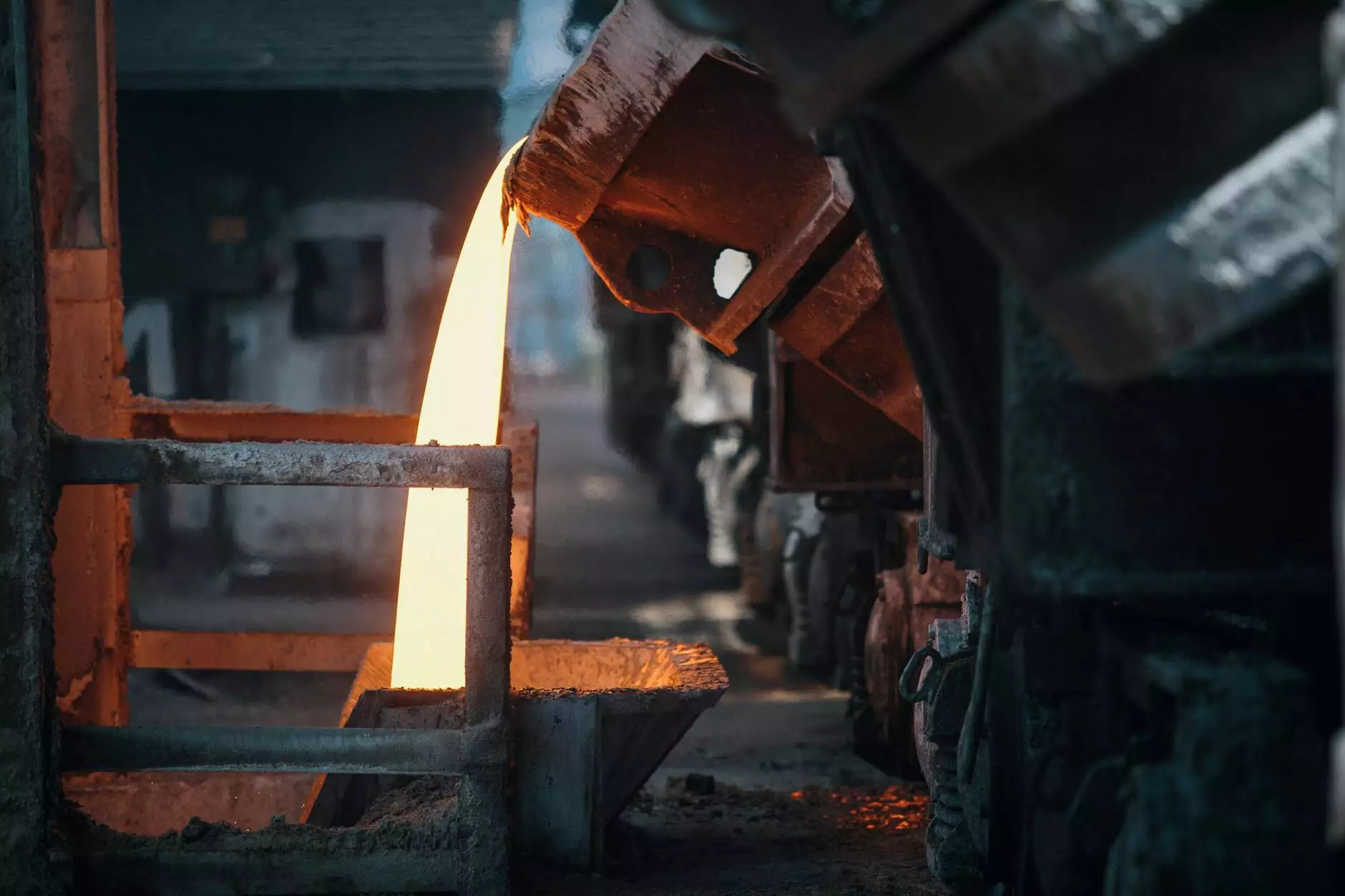
In the world of manufacturing, metal fabrication plays a critical role across various industries. A die casting parts factory stands at the forefront of this innovative process, providing high-quality components that meet the diverse needs of businesses around the globe. This article dives deep into the operations, benefits, and advancements related to die casting and how DeepMould excels in this field.
What is Die Casting?
Die casting is a manufacturing process that involves forcing molten metal under high pressure into a mold cavity, which is designed to form a desired shape. This method is widely used for producing parts with intricate shapes and dimensional accuracy. The die casting process is particularly favored for its ability to produce large volumes of parts with consistent quality and precise specifications.
Key Benefits of Die Casting
- High Precision: Die casting allows for tight tolerances and uniformity, essential for high-end applications in industries such as automotive, aerospace, and electronics.
- Cost-Effective: Once the initial mold is created, the cost per unit decreases significantly, making it ideal for mass production.
- Versatility: A variety of materials, including aluminum, zinc, and magnesium, can be utilized for different applications, making it a flexible manufacturing solution.
- Excellent Surface Finish: Parts produced through die casting can achieve an exceptional surface finish, minimizing the need for additional machining or polishing.
The Die Casting Process Explained
Understanding the die casting process is essential to appreciate the high-quality products produced in a die casting parts factory. Here’s a comprehensive step-by-step breakdown:
1. Die Preparation
The process begins with the creation of a die or mold. This is typically made from durable materials that can withstand the extreme temperatures and pressures involved in die casting. The design of the die is crucial, as it determines the shape and dimensions of the final product.
2. Melting the Metal
Once the die is prepared, the chosen metal alloy is melted in a furnace. This step requires precision, as the temperature must be controlled meticulously to achieve the correct viscosity and properties of the molten metal.
3. Injection of Molten Metal
After reaching the desired temperature, the molten metal is injected into the die under high pressure. This high-pressure application ensures that the metal fills every cavity, allowing for the creation of complex shapes.
4. Cooling and Solidification
Once the molten metal fills the die, it is allowed to cool and solidify. This process can take anywhere from a few seconds to several minutes, depending on the thickness and material of the cast.
5. Ejection of the Casting
After solidification, the die is opened, and the finished part is ejected. The precision of this step is vital to avoid any damage to the part or the die itself.
6. Finishing Operations
Even though die casting provides an excellent surface finish, some parts may require secondary operations, such as machining, drilling, or polishing, to meet specific standards and tolerances.
The Role of the Die Casting Parts Factory in Manufacturing
A die casting parts factory, like DeepMould, plays a pivotal role in the manufacturing sector by offering customized solutions to various industries. Here’s how our factory stands out:
Quality Assurance
At DeepMould, quality is our utmost priority. We implement stringent quality control measures at every stage of the die casting process. This includes:
- Material Inspection: All raw materials are thoroughly inspected for quality before being used in production.
- Process Monitoring: Advanced monitoring systems are employed to ensure that each casting meets the required specifications throughout the production run.
- Final Testing: Every finished product undergoes rigorous testing to ensure it meets performance and durability standards before being shipped.
Custom Solutions
Understanding that each client has unique needs, our die casting parts factory offers tailored solutions. We collaborate closely with clients from the design phase to production, ensuring that every project aligns with their specific requirements. Our custom solutions include:
- Prototype Development: Before final production, we offer prototype services to test designs and specifications.
- Material Selection: We assist clients in selecting the right materials for their applications, ensuring optimal performance and cost-effectiveness.
- Rapid Turnaround: With a well-equipped facility and skilled workforce, we ensure that projects are completed quickly without compromising quality.
Advanced Technology and Innovation
To remain competitive in this fast-paced industry, our factory continually invests in the latest technology and processes to enhance efficiency and reduce costs. This includes:
- Computer-Aided Design (CAD): Allows for precise planning and visualization of parts before they are manufactured.
- Robotic Automation: Speeds up production times while maintaining accuracy, especially in high-volume orders.
- Environmental Sustainability: We adopt eco-friendly practices, including recycling scrap metal and minimizing waste.
Industries We Serve
The versatility of our die casting processes enables us to serve a multitude of industries. Here are some of the sectors that benefit from our services:
1. Automotive Industry
The automotive industry relies heavily on die casting for producing engine blocks, transmission cases, and various structural components. Our factory provides components that meet the rigorous standards of safety and performance required in this sector.
2. Aerospace Sector
In the aerospace sector, where weight and strength are crucial, die casting offers an ideal solution. We produce lightweight and durable parts suitable for aircraft and spacecraft, contributing to improved fuel efficiency and performance.
3. Electronics and Electrical Appliances
Our products are also widely used in the electronics industry for housing, heat sinks, and other components. The precise manufacturing techniques ensure that parts fit seamlessly within complex electronic systems.
4. Medical Devices
We provide die-cast parts for medical devices, where quality and precision are non-negotiable. Our commitment to high standards assures clients of reliability and safety in life-saving equipment.
Why Choose DeepMould as Your Die Casting Partner?
Choosing the right manufacturer for your die casting needs can significantly impact the success of your projects. Here are compelling reasons to partner with DeepMould:
Expertise and Experience
With years of experience in the industry, our team of experts brings invaluable knowledge and skills to every project. We understand the nuances of die casting that can make or break a manufacturing process.
Unwavering Commitment to Quality
Our factory thrives on an ingrained culture of quality. Every employee shares the vision of providing only the best products to our clients.
Outstanding Customer Service
We prioritize communication and transparency. Our customer service team is always available to address inquiries and provide updates throughout the manufacturing process.
Conclusion
The landscape of manufacturing demands precision, efficiency, and quality, and a die casting parts factory like DeepMould is integral to meeting these expectations. With exceptional processes, custom solutions, and a commitment to excellence, we are proud to be a leader in the die casting industry. As we continue to innovate and adapt, we look forward to providing our partners with the best in metal fabrication and die casting solutions.
Explore how our expertise can benefit your next project by contacting us today! Together, we can forge a path to excellence in manufacturing.