The Versatile World of Dip Molding: A Game Changer for Electronics and Medical Supplies
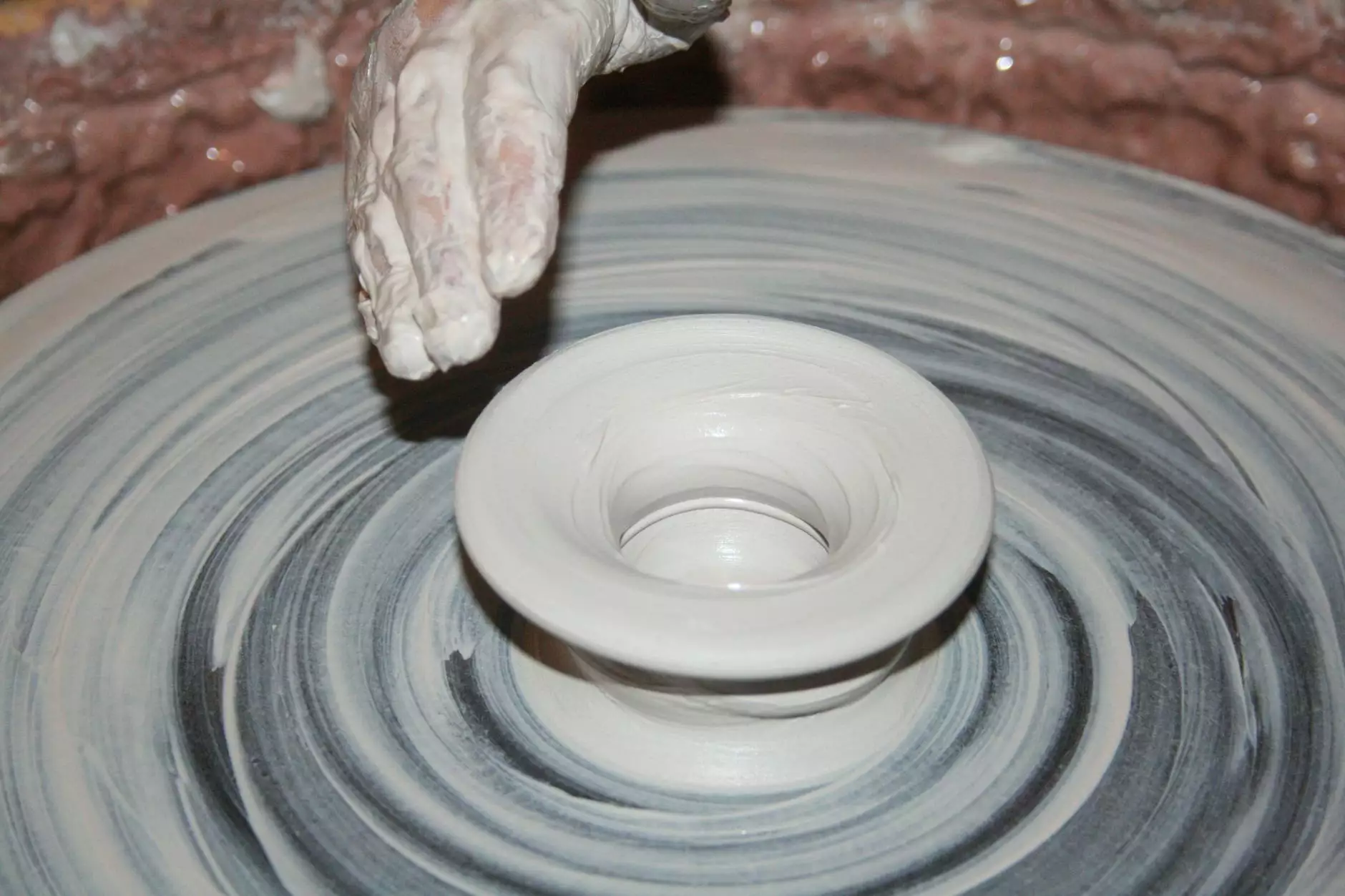
In the realm of modern manufacturing, dip molding stands out as a transformative process that caters to a multitude of industries, primarily electronics and medical supplies. It not only allows manufacturers to produce intricate designs that are functional and aesthetically pleasing but also significantly enhances product durability and reliability. In this article, we will delve into the intricacies of dip molding, its applications, and how companies like Nolato utilize this method to innovate and lead the market.
What is Dip Molding?
Dip molding is a manufacturing technique that involves immersing a mold into a heated polymer or elastomer material to create a coating or a product. This technique is particularly beneficial for producing items that require a robust and customizable finish. The process can be broken down into several key stages:
- Mold Preparation: Molds are typically made of aluminum or steel and are designed to create the desired shape of the product.
- Dipping: The prepared mold is dipped into a tank filled with heated liquid plastic or rubber, which adheres to the surface of the mold.
- Cooling: After the dipping, the coated mold is cooled, allowing the material to solidify and take the shape of the mold.
- Demolding: Once the material has cooled, it is removed from the mold, resulting in a finished product that showcases precision and quality.
The Advantages of Dip Molding
Dip molding offers a myriad of advantages that make it a preferred choice for manufacturers in various sectors, including:
- Cost-Effective Production: The process requires minimal tooling and equipment, reducing overall manufacturing costs.
- Customizable Options: With dip molding, manufacturers can easily alter the thickness, texture, and color of the products, catering to specific client needs.
- Durability and Protection: Products made through dip molding exhibit a high level of durability, providing essential protection against environmental factors and wear.
- Versatility: Dip molding can be used to produce a vast range of components, from simple grips to complex electrical insulators, making it suitable for many applications.
Applications of Dip Molding in Electronics
The electronics industry benefits immensely from dip molding in several ways. Here are some notable applications:
1. Electrical Insulators
Electrical insulators are crucial for protecting electronic components from electrical hazards. Dip molding allows for the production of high-quality insulators that offer excellent electrical resistance and thermal stability.
2. Component Coatings
Many electronic devices require coatings to prevent moisture, dust, and other contaminants from infiltrating sensitive areas. Dip molding can produce tailored coatings that enhance the longevity and reliability of electronic gadgets.
3. Grip Handles and Covers
Devices ranging from tools to consumer electronics often feature grips and covers for user comfort. Dip molded grips provide ergonomic benefits while ensuring a firm hold and protecting the underlying components.
Applications of Dip Molding in Medical Supplies
In the medical supplies sector, dip molding plays a pivotal role in the development of critical products:
1. Medical Devices
Devices such as syringes, catheters, and various surgical instruments benefit from dip molding. This process allows for the creation of biocompatible coatings that reduce the risk of infection and enhance patient safety.
2. Protective Barriers
With the increasing focus on hygiene, dip molding is utilized to create protective barriers that safeguard healthcare professionals and patients alike. These barriers can be made to specific sizes and shapes to fit various types of medical equipment.
3. Customizable Medical Components
Dip molding allows for the production of personalized components that meet unique medical needs, ensuring better patient outcomes through tailored solutions.
The Role of Nolato in Dip Molding Innovation
Nolato, a leader in the dip molding industry, epitomizes excellence in the field by constantly innovating and enhancing the manufacturing process. The company invests heavily in research and development to push the boundaries of what's possible with dip molding. Here’s how Nolato sets itself apart:
1. Commitment to Quality
Nolato adheres to stringent quality control measures throughout the dip molding process, ensuring that every product meets the highest industry standards. Their focus on continuous improvement demonstrates their unwavering commitment to excellence.
2. State-of-the-Art Technology
Utilizing cutting-edge equipment and technology, Nolato enhances the precision of the dip molding process, leading to superior product outcomes. This investment in technology allows for faster production times and greater customization options.
3. Sustainable Practices
Nolato is dedicated to sustainability and minimizing environmental impact. They implement eco-friendly materials and processes in their dip molding operations, aligning with global sustainability goals.
Future Trends in Dip Molding
As industries continue evolving, so too does the role of dip molding. Here are some expected trends that will shape the future of this manufacturing technique:
1. Advancements in Materials
The development of new, high-performance materials will enhance the versatility of dip molding, allowing for products that are not only stronger but also more adaptable to specific needs within the electronics and medical sectors.
2. Increased Automation
Automation in dip molding processes is expected to increase efficiency and precision, reducing the potential for human error and enabling manufacturers to scale production more rapidly while maintaining quality standards.
3. Focus on Custom Solutions
As consumer preferences continue to shift towards customized products, the demand for dip molding solutions that cater to specific client needs will grow. Companies will need to be agile and responsive to these trends to maintain their competitive edge.
Conclusion
In summary, dip molding represents a pivotal advancing in the manufacturing landscape, particularly within the electronics and medical supplies sectors. Its cost-effectiveness, versatility, and ability to produce high-quality, customized products make it an invaluable process. Companies like Nolato are at the forefront of this innovation, setting standards that others aspire to achieve. As the industry continues to evolve, the importance of dip molding in creating advanced, reliable products cannot be overstated. Embracing this process offers an opportunity for manufacturers to enhance product functionality and performance while meeting the dynamic needs of consumers and industries alike.