Understanding the Role of a CNC Parts Supplier in Metal Fabrication
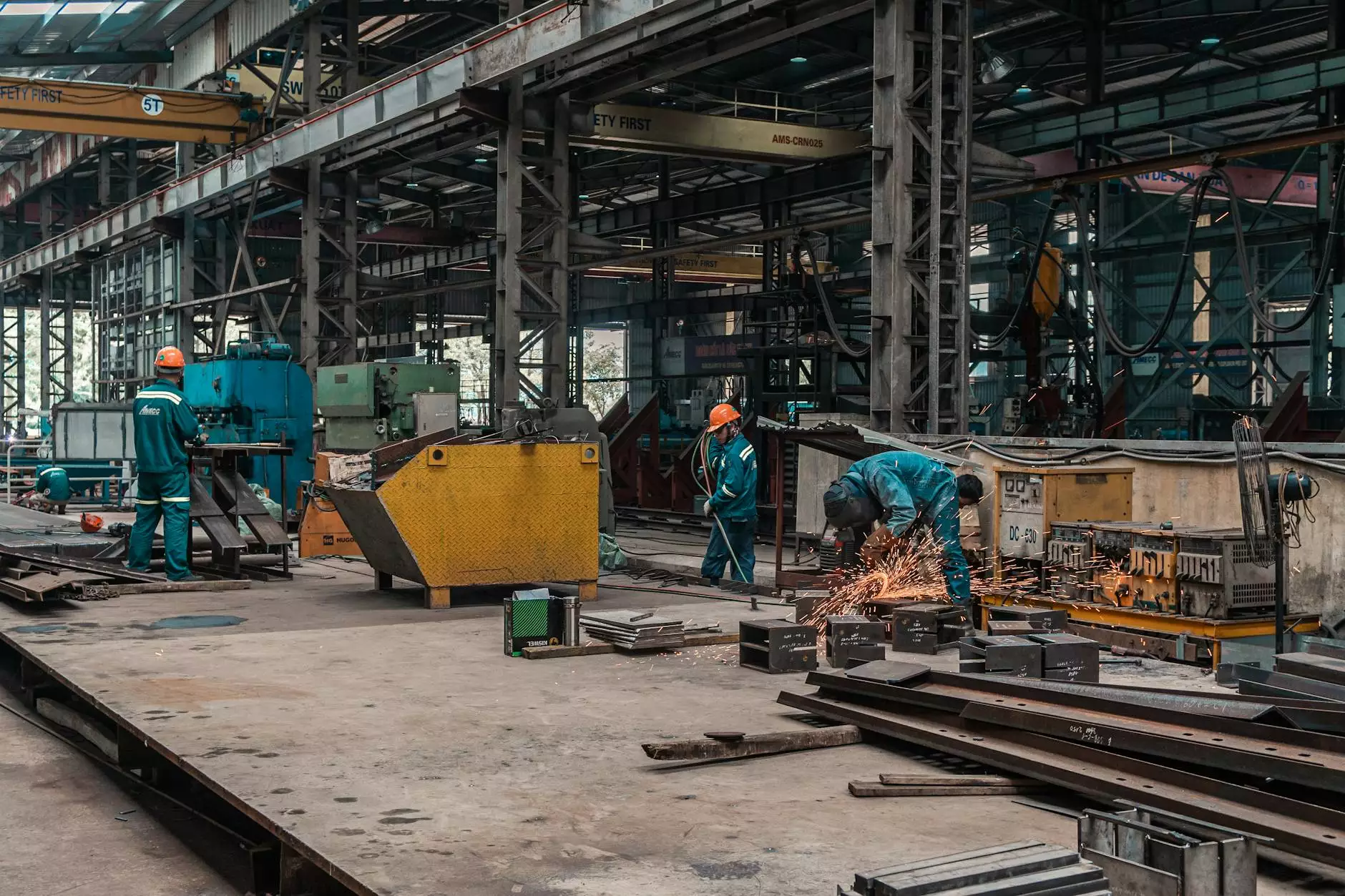
In today’s competitive manufacturing landscape, the demand for precision and efficiency is higher than ever. A CNC parts supplier plays a pivotal role in meeting these demands, especially for businesses in the metal fabricators category. This article will delve deep into the advantages of collaborating with a CNC parts supplier, the selection criteria to consider, and how to leverage these partnerships to optimize your fabrication processes and overall business success.
What is a CNC Parts Supplier?
A CNC parts supplier specializes in providing components that are manufactured using Computer Numerical Control (CNC) machining. This process involves the precise cutting, shaping, and finishing of materials, primarily metals, using automated tools. The result is high-quality parts that meet strict tolerances, making it essential for businesses that value precision and quality.
Advantages of Partnering with a CNC Parts Supplier
Choosing to work with a CNC parts supplier can bring numerous benefits to your business.
- Precision and Quality: CNC machining allows for extremely tight tolerances, ensuring that each part meets the exact specifications required for optimal performance.
- Customization: CNC suppliers can produce custom parts based on your specifications, giving you the flexibility to design products that cater specifically to your market needs.
- Cost Efficiency: By utilizing a CNC parts supplier, businesses can reduce the costs associated with in-house production, such as labor, overhead, and tooling.
- Scalability: As your business grows, CNC suppliers can scale production to meet increasing demands without compromising quality.
- Quick Turnaround Times: CNC machining processes are highly efficient, allowing for shorter lead times and faster project completion compared to traditional manufacturing methods.
Key Considerations When Selecting a CNC Parts Supplier
When looking for a reliable CNC parts supplier, several key factors should be evaluated to ensure that they align with your business goals:
- Experience and Expertise: Look for suppliers with experience in your specific industry and knowledge of the materials used.
- Quality Certifications: Ensure the supplier has quality management systems in place such as ISO certification, which guarantees adherence to international standards.
- Capability and Technology: Assess the technology and machinery the supplier uses. Modern CNC machines can lead to better precision and efficiency.
- Range of Services: Consider suppliers that offer a variety of services including design assistance, prototyping, and assembly.
- Customer Support: Strong communication and support are essential for a successful business relationship. A good supplier should be responsive to inquiries and proactive in problem-solving.
How CNC Parts Suppliers Enhance Metal Fabrication Processes
Working with a skilled CNC parts supplier can significantly enhance metal fabrication processes in various ways:
Streamlined Production Workflow
By outsourcing parts manufacturing to a CNC supplier, metal fabricators can focus their internal resources on core competencies like assembly and customer service, leading to a more streamlined workflow.
Access to Advanced Technologies
CNC suppliers often invest in the latest technologies. By partnering with them, metal fabricators can benefit from these advancements without the capital expenditure required to maintain such equipment in-house.
Improved Innovation
Collaborating with a CNC parts supplier can lead to improved innovation as they often have insights into the latest trends and manufacturing processes that can give your business a competitive edge.
Case Studies: Success Stories of CNC Parts Suppliers in Metal Fabrication
To illustrate the impact of CNC parts suppliers on metal fabrication, let's look at a couple of successful collaborations:
Case Study 1: Automotive Component Manufacturing
An automotive company faced challenges in meeting production demands for a new model. They partnered with a CNC parts supplier to produce critical engine components. By leveraging the supplier’s capabilities, the company was able to reduce costs by 30% and increase production speed, allowing them to meet market demands and launch their product ahead of competitors.
Case Study 2: Aerospace Parts Production
An aerospace manufacturer was in need of highly precise components for their aircraft. They sought a CNC parts supplier known for their advanced machining technology. The supplier provided parts that met stringent regulatory standards and helped the manufacturer reduce weight in their designs, contributing to fuel efficiency and cost savings in operation.
Cost Considerations and Budgeting for CNC Parts Procurement
Understanding the costs associated with procuring CNC parts is vital for budgeting and financial planning. Here are some key components to consider:
- Material Costs: The type of material (aluminum, steel, titanium) significantly impacts pricing. Be sure to assess which materials are necessary for your project.
- Machining Complexity: More complex designs require longer machining times and may increase labor costs.
- Order Volume: Bulk orders often lead to cost savings, but it’s essential to predict demand accurately to avoid overproduction.
- Shipping and Handling: Logistics costs can add to the overall expense of procuring parts, especially for international suppliers.
Optimizing Collaboration with Your CNC Parts Supplier
To maximize the benefits of working with a CNC parts supplier, consider the following strategies:
- Develop Clear Specifications: Provide detailed drawings and specifications to avoid misunderstandings and ensure quality.
- Maintain Open Communication: Regular check-ins and updates can help align both parties on deadlines and expectations.
- Solicit Feedback: Encourage your supplier to provide insights on design improvements or material alternatives that could enhance product performance or reduce costs.
- Build a Long-Term Relationship: Fostering a partnership mentality can lead to better service and responses in times of urgent needs.
The Future of CNC Parts Supply and Metal Fabrication
The landscape of CNC parts supply is continuously evolving. Here are some trends that are shaping the future:
Integration of Automation and AI
With advancements in artificial intelligence and automation, CNC machining is becoming more efficient. Suppliers are looking to integrate AI into various processes to optimize production and reduce waste.
Increased Sustainability Efforts
As the emphasis on sustainability grows, CNC parts suppliers are focusing on eco-friendly practices, from material sourcing to waste management, ensuring environmentally responsible manufacturing.
Expansion of Digital Services
Many suppliers are incorporating digital services such as online ordering and real-time tracking, making it easier for businesses to manage their supply chains effectively.
Conclusion: The Importance of Choosing the Right CNC Parts Supplier
In the highly competitive realm of metal fabrication, selecting the right CNC parts supplier is crucial for maintaining a high standard of quality, efficiency, and innovation. By understanding the services they offer, evaluating their capabilities, and fostering strong collaborations, businesses can significantly enhance their operations and meet customer demands effectively.
For businesses looking to thrive in the evolving manufacturing landscape, partnering with a trusted CNC parts supplier like DeepMould can provide a robust foundation for success. Don't overlook the value that these partnerships bring in terms of cutting-edge technology, cost efficiencies, and product quality.