Unleashing the Power of a Plastic Injection Molder in Metal Fabrication
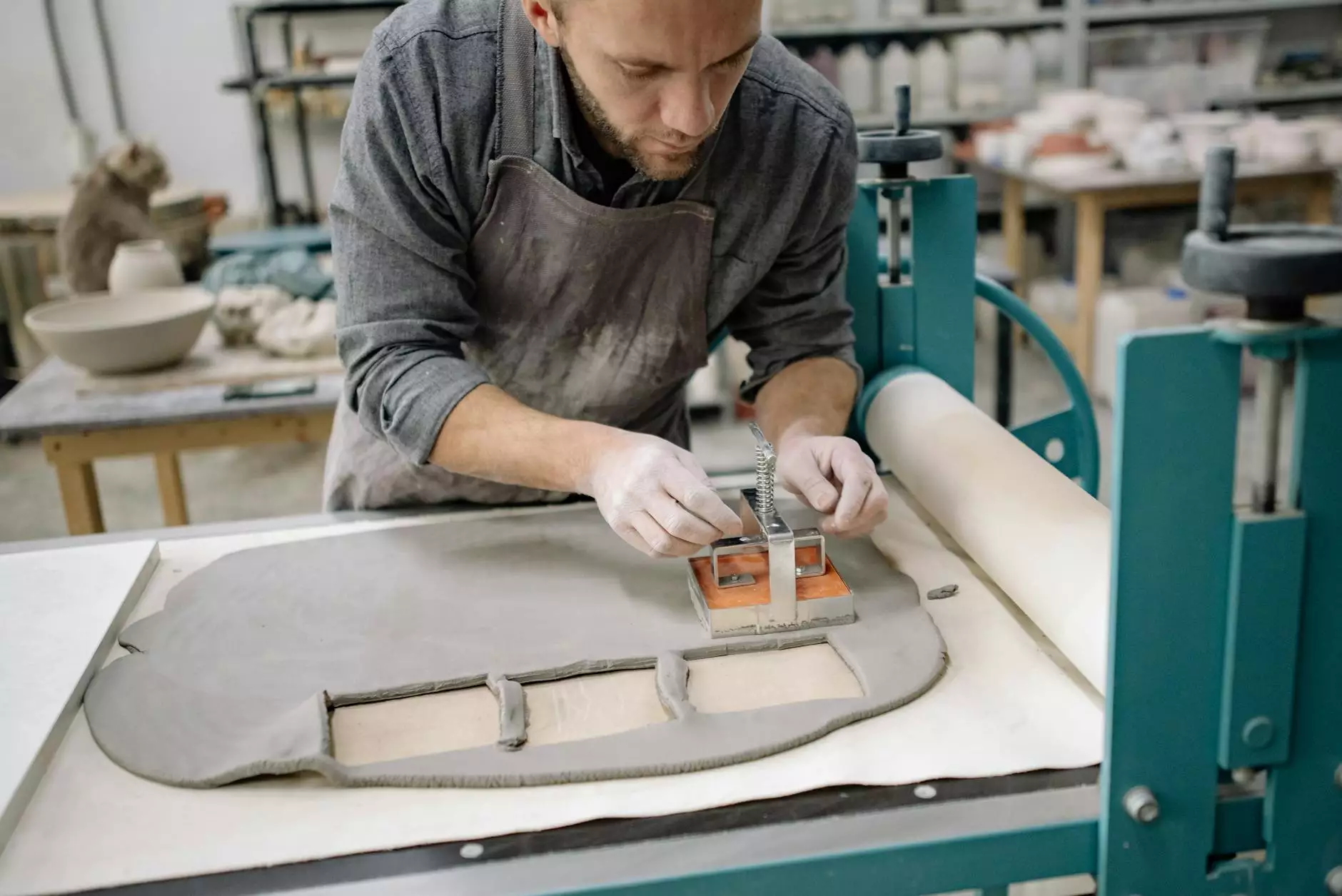
The world of manufacturing is ever-evolving, and as businesses strive to increase their productivity and efficiency, the role of advanced technologies cannot be overstated. One technology that has significantly transformed the landscape of metal fabrication is the plastic injection molder. This article delves deep into the nuances of plastic injection molding, its profound impact on metal fabrication, and how businesses like DeepMould are leveraging this technology to gain a competitive edge.
Understanding Plastic Injection Molding
Plastic injection molding is a manufacturing process used to create parts by injecting molten material into a mold. It is highly efficient and allows for the mass production of parts with high precision. The process begins with the following steps:
- Material Selection: The type of plastic resin is chosen based on requirements such as strength, flexibility, and temperature resistance.
- Heating: The plastic is heated until it reaches a molten state, making it suitable for injection.
- Injection: The molten plastic is injected into a closed mold at high pressure.
- Cooling: The injected material is allowed to cool and solidify in the mold.
- Demolding: The part is ejected from the mold after it has cooled sufficiently.
This method allows manufacturers to produce complex shapes and sizes with exceptional precision and repeatability, making it a cornerstone technique for industries including automotive, consumer goods, and, notably, metal fabrication.
The Role of a Plastic Injection Molder in Metal Fabrication
Metal fabricators increasingly rely on plastic injection molding for various applications that enhance their manufacturing capabilities. Here’s how:
1. Cost-Effectiveness
Utilizing a plastic injection molder can significantly reduce production costs. Here are key aspects:
- Reduced Material Waste: Molding processes optimize the amount of material used, minimizing scrap wastage.
- High Production Volume: Injection molding allows for the production of large quantities of parts in a shorter time frame, spreading costs over more units.
- Lower Labor Costs: The automation and efficiency of injection molding reduce the need for manual labor in the manufacturing process.
2. Enhanced Product Quality
Quality is paramount in metal fabrication, and the use of plastic injection molding contributes significantly:
- Precision Engineering: The ability to create parts with tight tolerances ensures that components fit perfectly in the final assembly.
- Uniformity: Each part produced is consistent, enhancing the overall aesthetic and functional quality of the final product.
- Versatility in Design: Designers have the freedom to create complex geometries that would be difficult, if not impossible, to achieve through traditional metalworking techniques.
Applications of Plastic Injection Molding in Metal Fabrication
The applications of plastic injection molding within the realm of metal fabrication are extensive:
1. Manufacturing of Components
Many components—such as housings, clips, and brackets—traditionally made from metal are now produced using high-strength plastics through injection molding. This shift not only reduces weight but also lowers manufacturing costs.
2. Prototyping
Injection molded parts can be rapidly produced for prototypes, allowing for faster iteration and testing of design concepts before moving to full-scale production. This agility is crucial in today’s fast-paced market.
3. Tooling and Fixtures
Complex tooling and fixtures can be created using plastic injection molding techniques, facilitating easier assembly and disassembly processes in metal fabrication operations.
Choosing the Right Plastic Injection Molder
Choosing the right plastic injection molder is crucial for optimizing the benefits of this process. Business owners should consider the following factors:
1. Experience and Expertise
Select manufacturers with proven experience in the industry and a solid understanding of both plastic materials and metal fabrication techniques.
2. Technology and Equipment
Investing in modern, advanced injection molding technology is vital for efficiency, precision, and the ability to produce high-quality parts. Look for companies using the latest machines and software for optimal production capabilities.
3. Material Knowledge
A reputable plastic injection molder should have extensive knowledge of various plastic materials and their properties to guide your choices based on your project requirements.
4. Customer Support
Strong customer support is essential, especially when navigating challenges that might arise during production. Look for companies that prioritize clear communication and customer satisfaction.
Future Trends in Plastic Injection Molding
The future of plastic injection molding looks promising, shaped by innovations and advancements in technology that will likely impact the metal fabrication industry:
1. Sustainable Practices
As industries shift towards sustainability, the plastic injection molding sector is embracing environmentally friendly practices, including:
- Biodegradable Materials: The use of biodegradable plastics is on the rise, allowing manufacturers to reduce their environmental footprint.
- Recycling Initiatives: Injection molding companies are now focusing on recycling scrap materials and using them in production processes.
2. Automation and Smart Manufacturing
The integration of smart technologies, such as IoT (Internet of Things) and AI (Artificial Intelligence), is transforming injection molding processes:
- Predictive Maintenance: AI can help predict machinery failures before they happen, minimizing downtime and maintenance costs.
- Real-time Monitoring: IoT devices can monitor processes in real-time, ensuring quality and efficiency throughout production.
3. Advanced Materials
The development of new advanced materials will continue to expand the capabilities of plastic injection molding. These materials may offer enhanced performance in terms of strength, heat resistance, and durability.
Conclusion: The Lasting Impact of a Plastic Injection Molder
As technology advances, the role of the plastic injection molder in metal fabrication will only intensify. From cost savings and quality enhancements to the capability of producing complex designs quickly, it is clear that this technology is an integral aspect of modern manufacturing.
Businesses looking to thrive in the competitive landscape of metal fabrication should consider the strategic incorporation of plastic injection molding into their processes. By harnessing the advantages of this technology, companies like DeepMould can streamline operations, enhance product quality, and ultimately contribute to a more innovative and sustainable future in manufacturing.